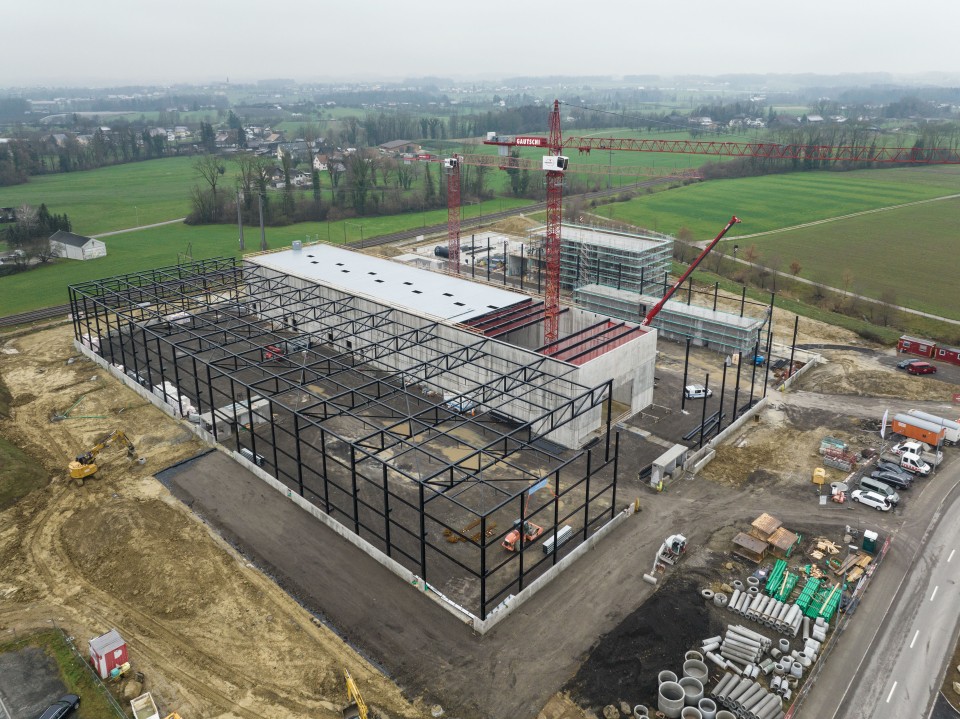
La Forster Profilsysteme AG si trasferisce a Romanshorn, nel Canton Turgovia: il campus Forster è il primo complesso di edifici commerciali in Svizzera a ricevere la certificazione LEED, conosciuta in tutto il mondo, di livello «Gold» per edifici particolarmente sostenibili. Debrunner Acifer ha fornito alla Ernst Fischer AG, che si occupava della costruzione, anche 600 t di Green Steel tagliato su misura e consegnato secondo distinte complete.
La Forster Profilsysteme AG sta costruendo a Romanshorn un campus da 52 milioni di franchi svizzeri per la sua nuova sede aziendale. Il campus Forster accoglierà i circa 140 dipendenti ora suddivisi nelle due sedi di Arbon. Definisce inoltre degli standard in materia di sostenibilità, sia nella costruzione che nel funzionamento. Per questo progetto pionieristico dal punto di vista ecologico Debrunner Acifer ha fornito, tra l'altro, 600 t di Green Steel.